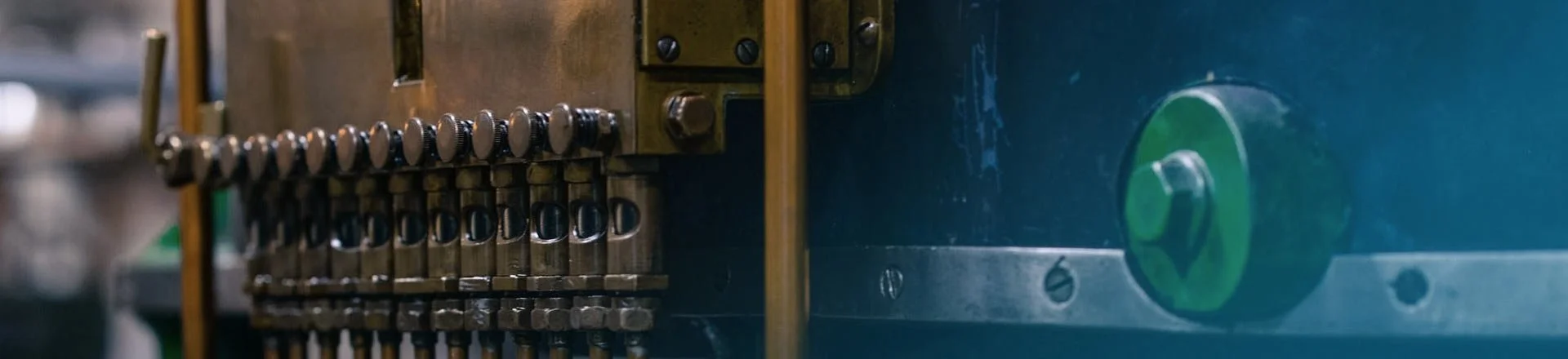
Letter From The President
One Quality Manufacturing From Diamond Standard One Brand – One Vision – One Mission
A Letter From Michael J. O’Neal, President of Diamond Standard Parts, LLC
The Diamond Standard Brand culture of quality is a commitment to the industry through ONE QUALITY MANUFACTURING that separates our manufacturing promise and delivery from ALL other manufacturers of alternative non-structural and structural parts for the North American market. One part quality and materials, no dual line substandard parts for other markets. This was the promise when we created the brand.
Diamond Standard Brand parts are third party comparatively tested and are designed, manufactured, and sold to perform in the same manner in a collision as the parts that came on the vehicle. We do not manufacture parts that do not meet this criteria. Comparative parts testing by MGA Research Corporation and CAPA are part of an extensive campaign of full accountability, repeatability and sustainability of the brand.
You can’t create the system that produces parts to perform in the same manner as the vehicle’s original collision management system without developing a “Culture of One Quality Manufacturing” in your team platform. Further, written sustainable policy goals that spell out what this means must be inherent in the QSM followed by all employees. Everyone must understand that there is no exception to the rule or bending of the plan.
Diamond Standard’s ongoing leadership in raising industry alternative quality parts standards and certifying of rear step bumper full assemblies and structural front bumpers, brackets, reinforcement bars, and absorbers by CAPA has created opportunities for other manufacturers to certify their parts of this type. The fact below the surface is that some of these manufacturers are the very companies that produce, manufacture and/or consolidate the same substandard parts that create the need for certification in the first place. Read this again…. How can this fact be ignored? The manufacture, existence and installation of substandard parts continues today based on price, not quality, driven models. Would it be permissible for a company to knowingly make a toy with lead based paint based on a price model to satisfy a segment for one market and have the same toy certified for the same market based on the correct safe paint used on the same part? In best cases a generic model of a product or private labeled product mimics in a similar manner the branded product that is by its design or material content more expensive. However, low cost and cheaper non-performing non-structural and structural parts in collision management systems should not be utilized and the manufacturers involved in the manufacture, sale or supply of them must be prohibited from certifying ANY parts as long as they are the source of and contributors to this problem but unfortunately are not, leaving the door open for substitution and fraud. The benefits to the industry adopting ZERO tolerance for a manufacturing group to attain certification of structural parts without a total commitment to the quality and integrity of structural parts for sale in the US and Canada are immense and numerous. The industry could benefit immediately by eliminating the possibility of part substitution of a substandard part for a certified part, eliminating the need and high cost of dual inventories at the distributor level and help reduce the number of collision total losses which continue to run chronically high.
Diamond Standard supports the Car Coalition, ABPA, ASA, SCRS, and continues to support the right to repair.
Thank you for your continued support of Diamond Standard,